Nevermind, turns out there were more posts I missed
Sent from my SM-N9005 using Tapatalk
CNC lightweight front spindles
Moderators: timk, Stu, -alex, miata, zombie, Andrew
- plohl
- Racing Driver
- Posts: 1922
- Joined: Wed Oct 14, 2009 12:13 am
- Vehicle: NA8
- Location: Brisbane
Re: CNC lightweight front spindles
Cheers,
plohl
plohl
-
- Racing Driver
- Posts: 1117
- Joined: Tue Dec 31, 2013 12:11 pm
- Vehicle: NA6
Re: CNC lightweight front spindles
I wasn't really planning on selling these, unless there is a big need within the community. I'm doing all this so that I can run them! I do like designing parts to be future proof though as I don't know which direction my car development will take me in the future.
The issue with the Keisler spindles is the change in geometry from the drop causing all sorts of issues with suspension setup. My design doesn't incorporate a drop for that reason, or if I do, it will be minor.
In terms of the steering arm tie rod, I was planning on running a rod end that threads onto the steering arm rather than the tie rod. This way I can pack the distance from the arm to the rack to alter bump steer. Also in terms of brake caliper... I am currently running Dynapro caliper but it would be cool to fit up AP or Stoptech calipers. If I make the caliper mount interchangeable though I could switch it out when I want.
The issue with the Keisler spindles is the change in geometry from the drop causing all sorts of issues with suspension setup. My design doesn't incorporate a drop for that reason, or if I do, it will be minor.
In terms of the steering arm tie rod, I was planning on running a rod end that threads onto the steering arm rather than the tie rod. This way I can pack the distance from the arm to the rack to alter bump steer. Also in terms of brake caliper... I am currently running Dynapro caliper but it would be cool to fit up AP or Stoptech calipers. If I make the caliper mount interchangeable though I could switch it out when I want.
NA8: N/A 200whp | Haltech | Skunk2 Intake | S90 TB | RCP | 5 speed c/r dogbox | 4.78 diff | AST Shocks
Barbs L: 64.12 | S: 58.62 | Collie: 49.72
Barbs L: 64.12 | S: 58.62 | Collie: 49.72
- hks_kansei
- Speed Racer
- Posts: 6154
- Joined: Tue Feb 03, 2009 10:43 am
- Vehicle: NB8A
- Location: Victoria
Re: CNC lightweight front spindles
I thought the point of drop spindles was to allow. Ride height drop while leaving geometry intact?
Since the mounts etc stay the same, just the wheel center point is higher on the knuckle.
Since the mounts etc stay the same, just the wheel center point is higher on the knuckle.
1999 Mazda MX5 - 1989 Honda CT110 (for sale) - 1994 Mazda 626 wagon (GF's)
- zossy1
- Racing Driver
- Posts: 1979
- Joined: Wed Aug 18, 2010 8:48 am
- Vehicle: NA8
- Location: Southern Highlands, NSW
- Contact:
Re: CNC lightweight front spindles
The Keislers do 4 things, in order of importance:
1. Build ideal caster/camber adjustment into the central areas of the alignment window (ie. You get pretty much perfect alignment numbers at the middle of your alignment pills, giving much better adjustability)
2. Lower front roll centre
3. Reduce bump steer
4. Reduce camber gain on bump
The rears do similar - but are even more of a pain to get right than the fronts.
1. Build ideal caster/camber adjustment into the central areas of the alignment window (ie. You get pretty much perfect alignment numbers at the middle of your alignment pills, giving much better adjustability)
2. Lower front roll centre
3. Reduce bump steer
4. Reduce camber gain on bump
The rears do similar - but are even more of a pain to get right than the fronts.
-
- Racing Driver
- Posts: 1052
- Joined: Sun Oct 07, 2012 10:51 am
- Vehicle: NA8
- Location: Brisbane Southside
Re: CNC lightweight front spindles
These comments may be past use by date but am fascinated today by the innovative ideas presented.
Option 1:
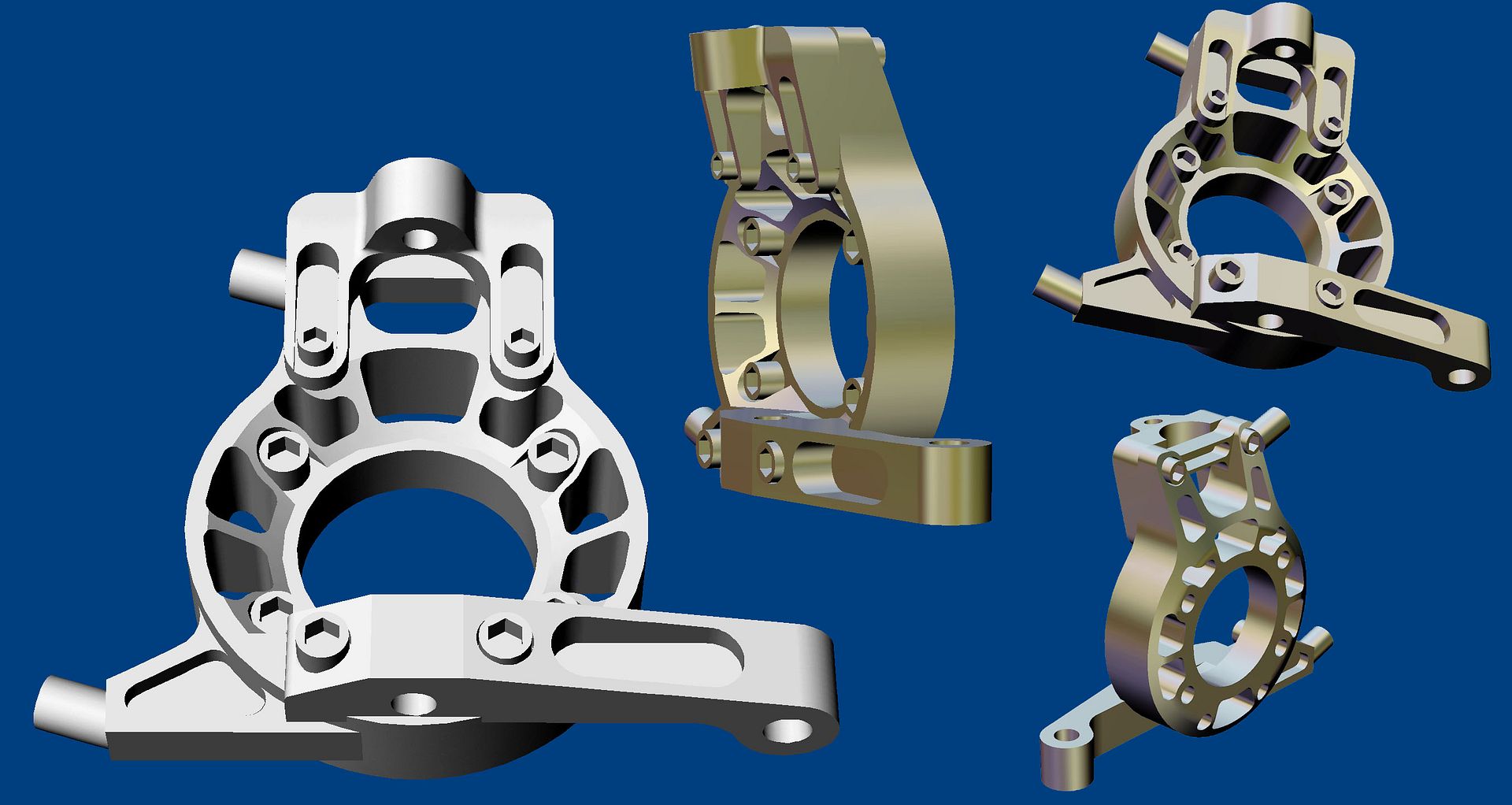
Option 2:
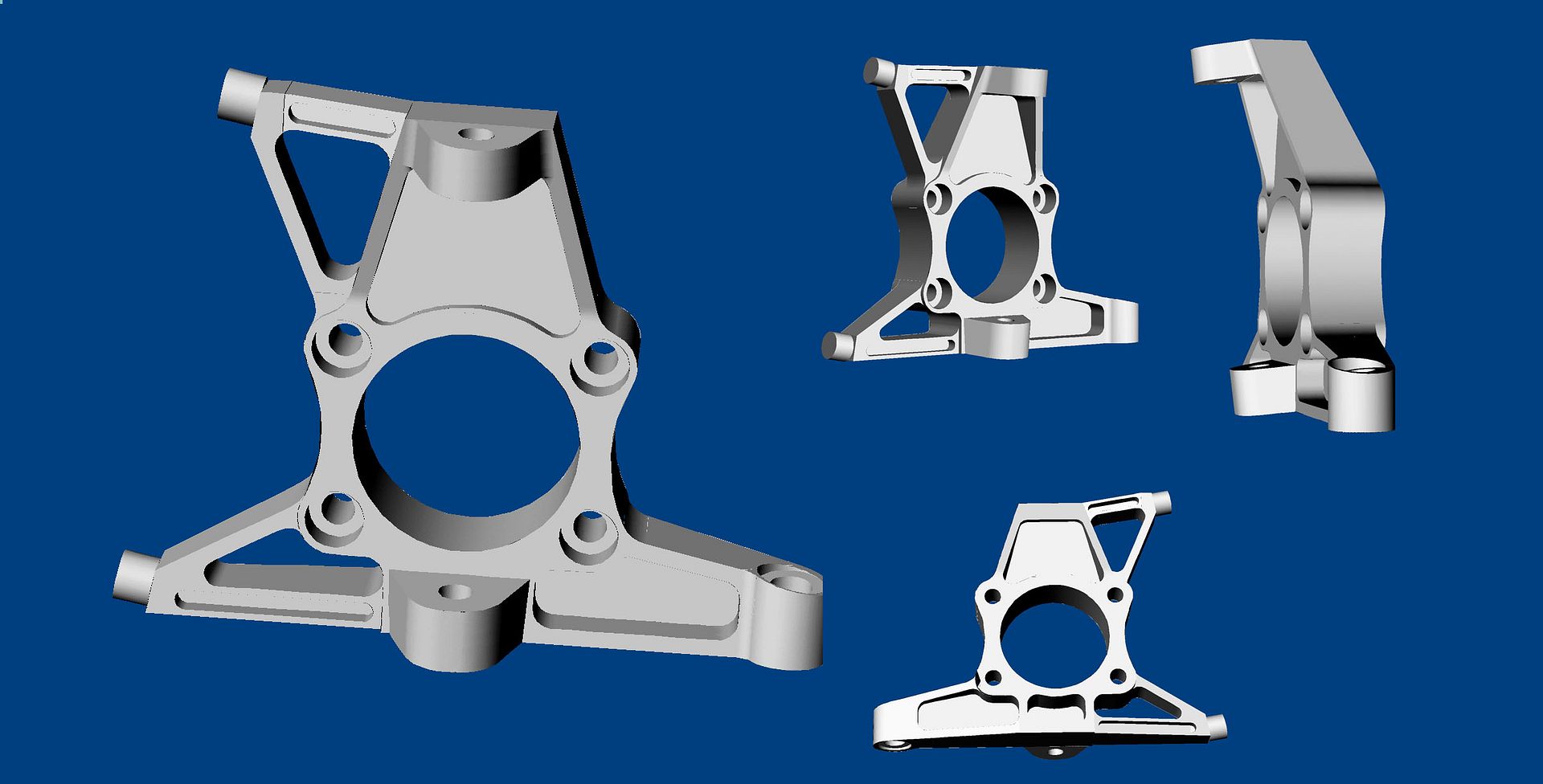
I like the combined bolt on pitman arm and lower ball joint mount of Option 1.
It would need some decent bolts as long as possible and thick joint faces at the bolts to keep the joint under the bolts locally very stiff but both items need to be chunky in this area anyway and thickness can wash out quickly away from the bolts.
Suggest pitman arm be rotated through 90 degrees so its depth as a cantilever beam is in the plane of the steering loads.
Look at using say 3 pitman arm bolts...2 on the right and 1 on the left as right side carries approx twice steering load as the left side. Add a 4th to ensure friction grip for vertical loads.
The joint should be designed friction grip so no bolts in shear. Removable dowels for first up locating only. Maybe the assembly could bolt up from underneath also.
I caution against the twin annulus structure separated by little webs in Option 1. I think the Option 2 structure is much simpler and stress gradients through the structure much easier to determine. You know all the loads are more directly connected so stress paths not broken up into traversing through a maze of different paths fighting each other because of Poisson's Ratio and Hooke's Law determining load paths.
May be better to have the outside annulus for brake ducting a separate lightweight attachment.
I cannot imagine Option 1 structure being efficient with a lot of potential for hot spots and cold spots in an FEA, both annoying for different reasons. Much easier I think to sculpt Option 2 into a structure having metal where it matters to achieve an FEA all the one colour.
Option 1:
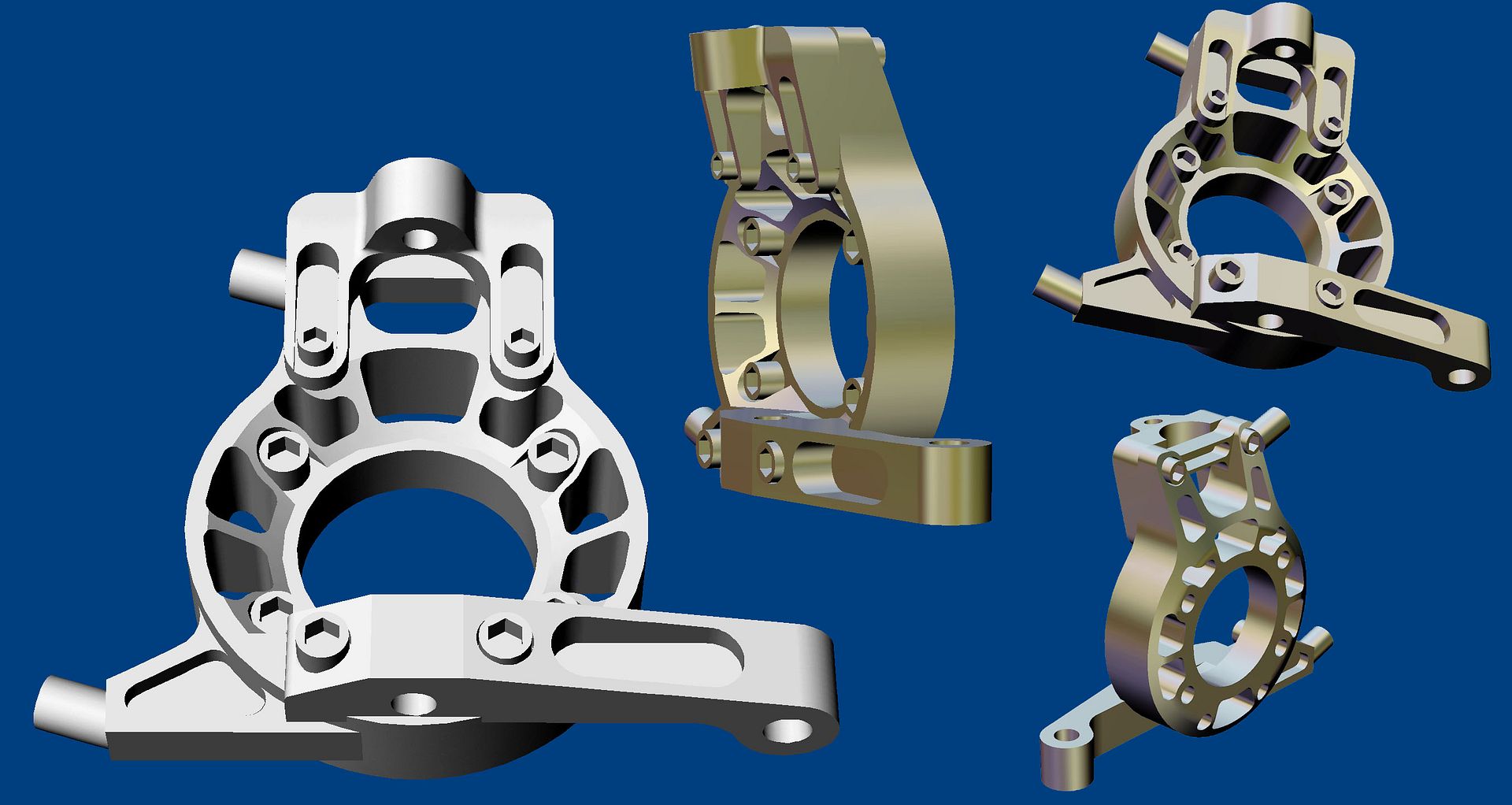
Option 2:
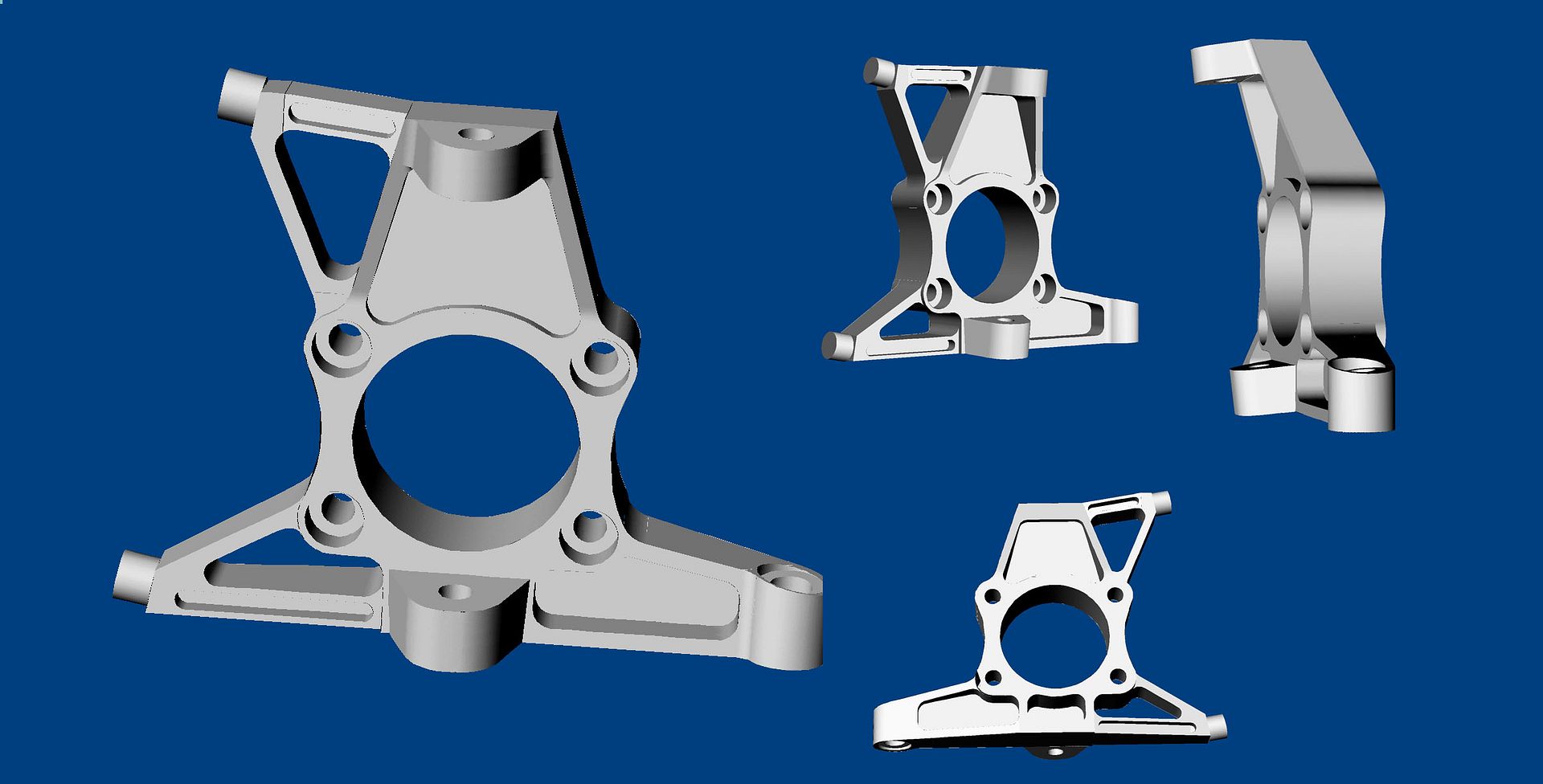
I like the combined bolt on pitman arm and lower ball joint mount of Option 1.
It would need some decent bolts as long as possible and thick joint faces at the bolts to keep the joint under the bolts locally very stiff but both items need to be chunky in this area anyway and thickness can wash out quickly away from the bolts.
Suggest pitman arm be rotated through 90 degrees so its depth as a cantilever beam is in the plane of the steering loads.
Look at using say 3 pitman arm bolts...2 on the right and 1 on the left as right side carries approx twice steering load as the left side. Add a 4th to ensure friction grip for vertical loads.
The joint should be designed friction grip so no bolts in shear. Removable dowels for first up locating only. Maybe the assembly could bolt up from underneath also.
I caution against the twin annulus structure separated by little webs in Option 1. I think the Option 2 structure is much simpler and stress gradients through the structure much easier to determine. You know all the loads are more directly connected so stress paths not broken up into traversing through a maze of different paths fighting each other because of Poisson's Ratio and Hooke's Law determining load paths.
May be better to have the outside annulus for brake ducting a separate lightweight attachment.
I cannot imagine Option 1 structure being efficient with a lot of potential for hot spots and cold spots in an FEA, both annoying for different reasons. Much easier I think to sculpt Option 2 into a structure having metal where it matters to achieve an FEA all the one colour.

Return to “MX5 Wheels, Suspension, Brakes & Tyres”
Who is online
Users browsing this forum: No registered users and 5 guests