My Audio install, Fibreglassing (lots of pics)
Posted: Sun Aug 19, 2007 3:53 am
Ok it's been a while since I have had an update and I've been teasing a few other forum members with promises that I would have it finished a few weeks ago well it looks like it's going to be at least another 4 weeks off
But just to prove I am actually doing something here is an update and a writeup on making a fibreglass subwoofer enclosure, all DIY
The gear
Headunit: Kenwood KDC-MP6533
Front stage: Jaycar 6.5\" Kevlar splits 75WRMS, CS2329
Rear: Jaycar 6x9\" Kevlar coaxials 80WRMS, CS2328
Amplifier: Jaycar 4x100WRMS Digital car amplifier, AA0425
Amplifier: Jaycar Monoblock 800WRMS D class
Subwoofer: Jaycar 10\" Carbon Fibre Sub
Now for the sub enclosure write-up
Took a look at possible places to put a sub and decided it would be in one of the wells at either side of the boot, figured I would be using the cubby on the passenger side quite often so the enclosure would be going over the battery. A false floor was made with removeable panels on either side of the boot, one for the cubby, the other providing access to the battery.
1. The area to be fibreglassed was masked up using painters masking tape (3M), this was followed by a layer of foil held onto the surface by double sided tape, and another layer of masking tape since fibreglass sticks to the paper better than exposed foil.
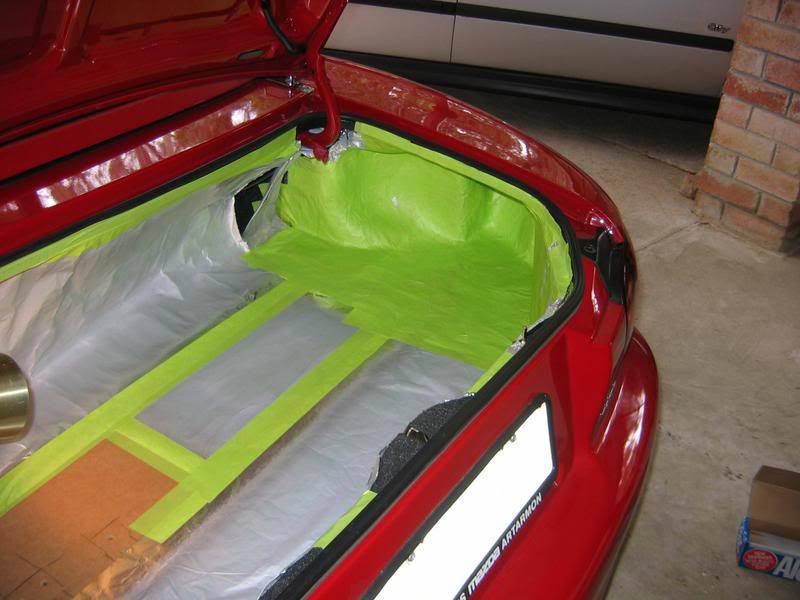
2. First layer of fibreglass. Found that the easiest way was using strips of matting about 5x30cm starting from the bottom and working up. Resin applied using a paint brush in a dabbling motion (imaging trying to use the brush end to stab the matting into position).
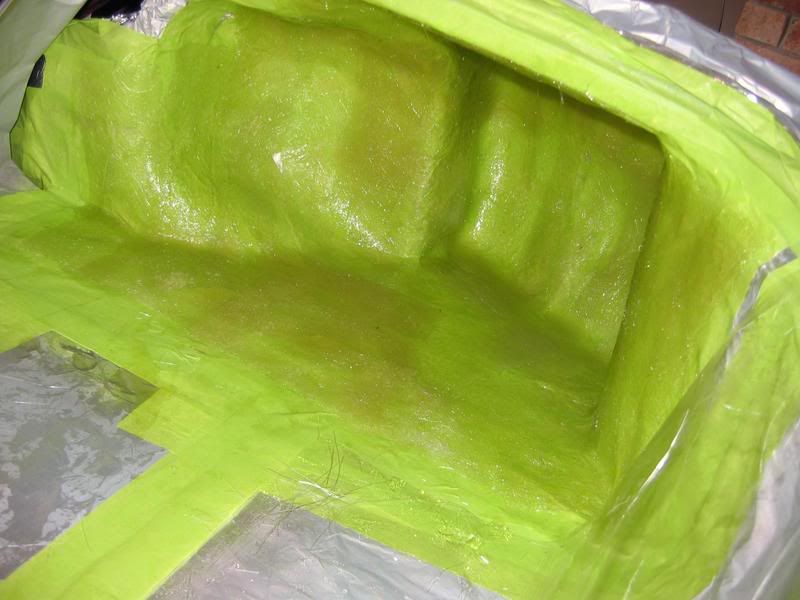
3. The mould was removed, here you can see how the foil was used making it easier to remove.
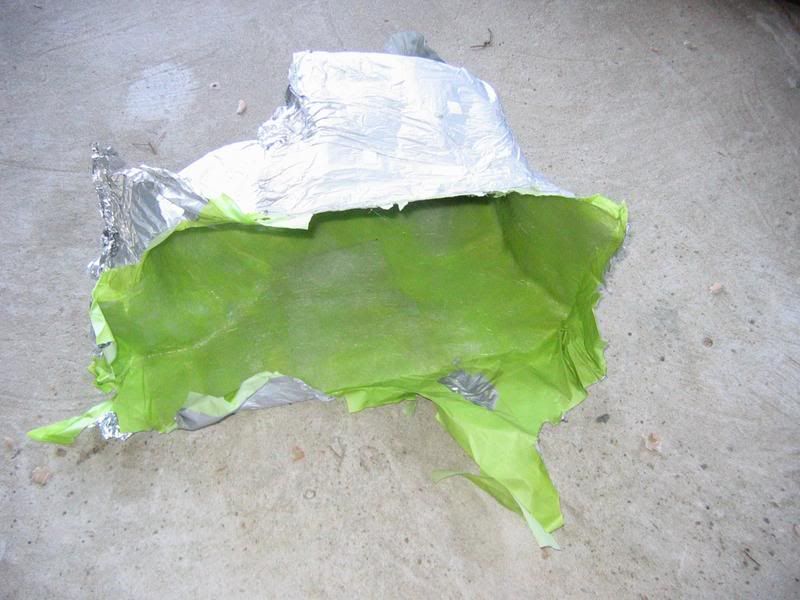
4. After removing the foil and masking tape the mould was revealed and test fitted.
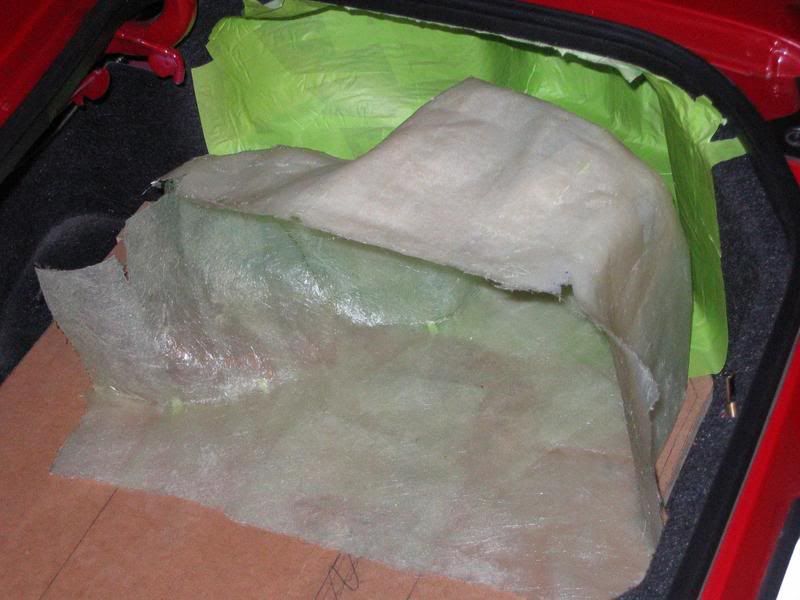
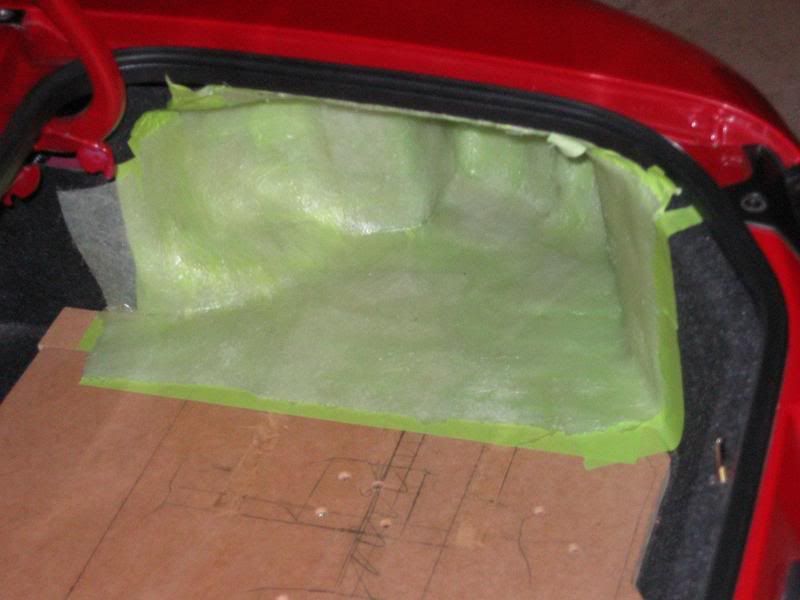
5. Skipped a few steps here, rings of MDF were made up, one for the sub to mount onto and another to go around the outside edge for a flush fit, these were then held in position using scrap pieces of MDF and a hot glue gun. Covered in a layer of flexible fabric stretched over the surface to be glassed and held in place but more hot glue, test fitted to make sure the boot would still open and close without problems. After all this a layer of resin was applied to the fabric without any fibreglass matting.
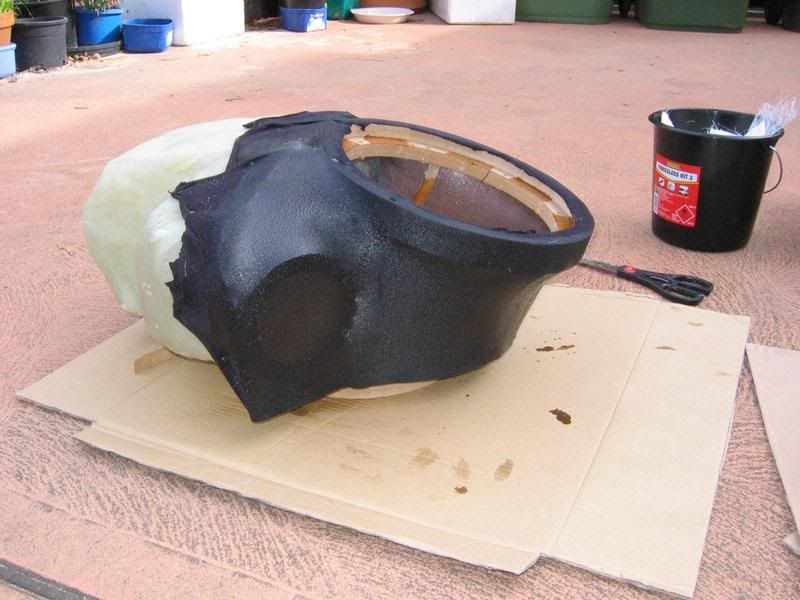
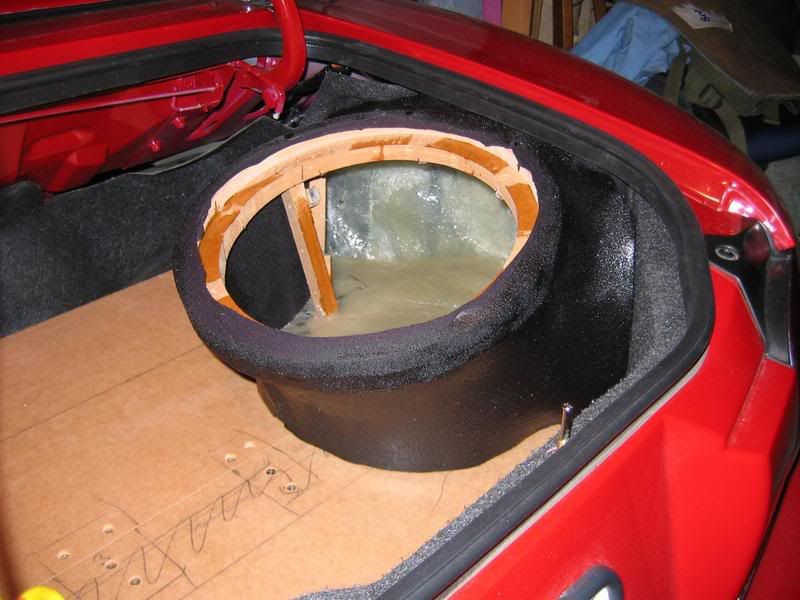
6. Many layers of fibreglass added to improve strength, most layers added from the inside via the sub hole to prevent adding to the exterior dimentions of the enclosure and comprimising the already perfect fit. Volume checked using filling from a bean bag.
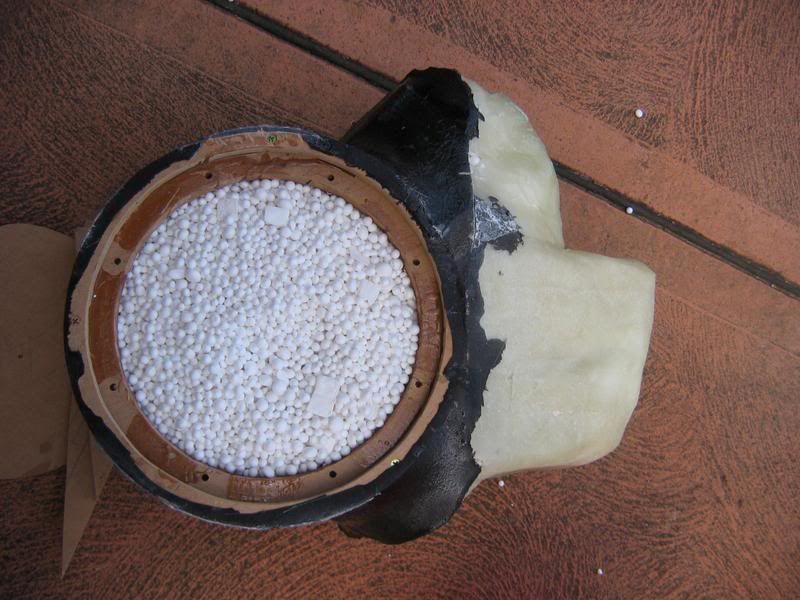
7. This photo highlights how the enclosure manages to take up minimal space while still having adequate internal volume.
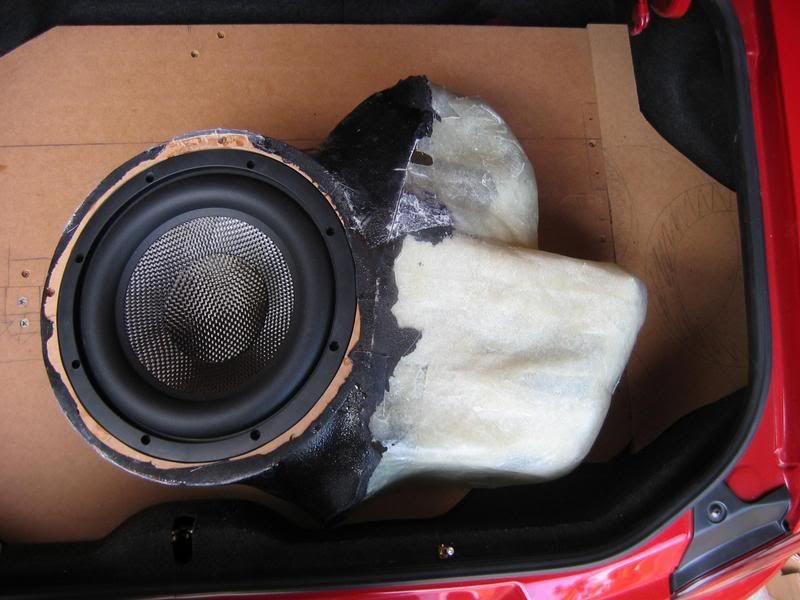
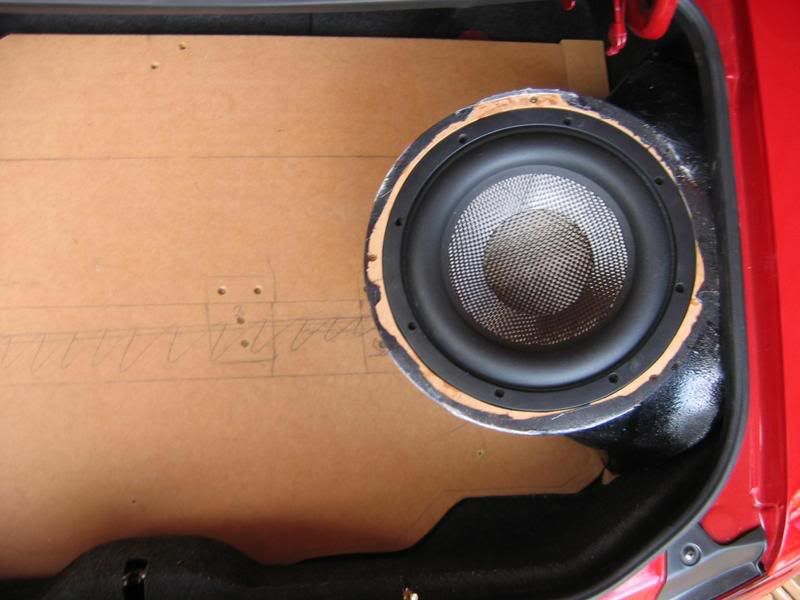
8. More layers of fibreglass added and a hole cut for the port.
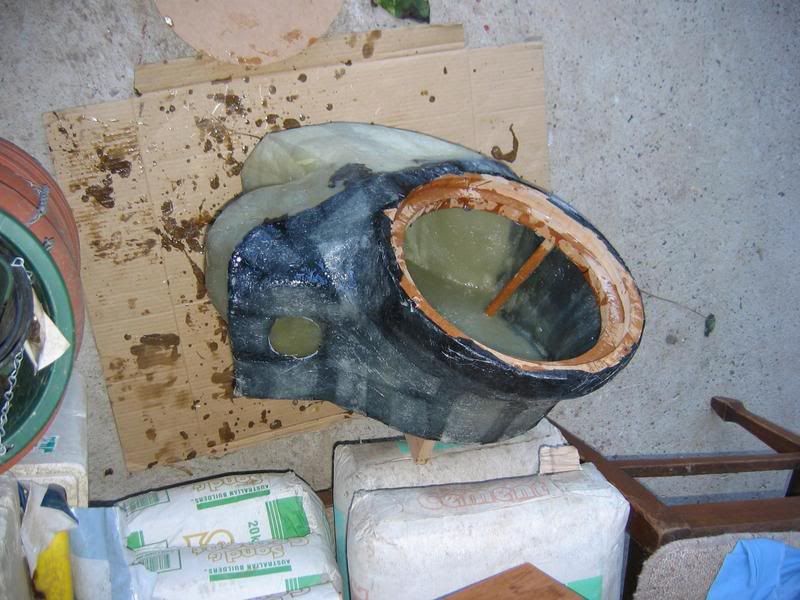
9. port added and a quick mock up with the sub in place.
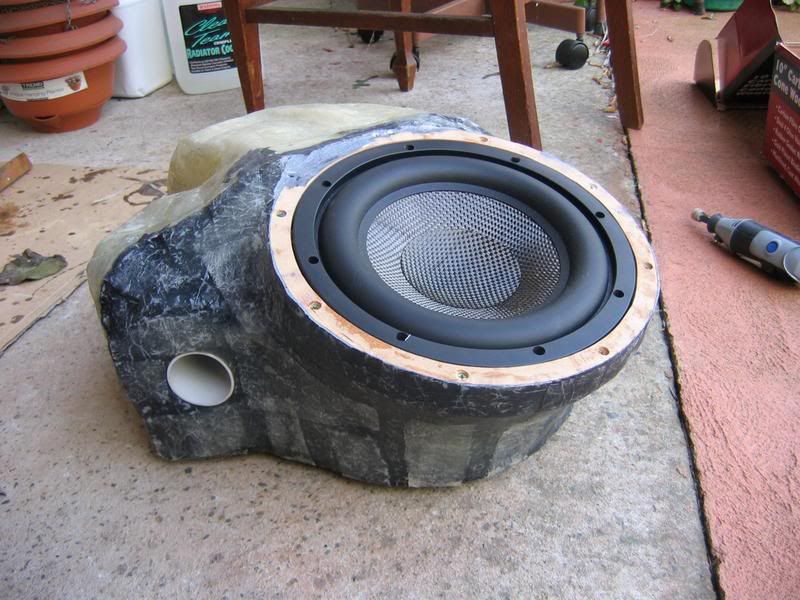
Tools required
Jigsaw for cutting MDF
scissors for cutting fibreglass matting
Dremel Router tool with sanding and cutting heads for trimming fibreglass that has set
Face mask, protecting from fumes and dust from fibreglass cutting and resins
Rubber gloves again protection from resin and fibreglass dust (it's itchy)
Things I learnt from all this
Buy from the specialists, Bunnings was great for getting the MDF and router but not so great for fibreglass 1kg was ~$55 at bunnings, in comparison 4kg with brushes mixing trays and great advice was ~$50 from FGI, a fibreglass company
There is more coming, the surface still needs to have more aesthetic appeal, amps need to be installed, and false floor covered.


But just to prove I am actually doing something here is an update and a writeup on making a fibreglass subwoofer enclosure, all DIY
The gear
Headunit: Kenwood KDC-MP6533
Front stage: Jaycar 6.5\" Kevlar splits 75WRMS, CS2329
Rear: Jaycar 6x9\" Kevlar coaxials 80WRMS, CS2328
Amplifier: Jaycar 4x100WRMS Digital car amplifier, AA0425
Amplifier: Jaycar Monoblock 800WRMS D class
Subwoofer: Jaycar 10\" Carbon Fibre Sub
Now for the sub enclosure write-up
Took a look at possible places to put a sub and decided it would be in one of the wells at either side of the boot, figured I would be using the cubby on the passenger side quite often so the enclosure would be going over the battery. A false floor was made with removeable panels on either side of the boot, one for the cubby, the other providing access to the battery.
1. The area to be fibreglassed was masked up using painters masking tape (3M), this was followed by a layer of foil held onto the surface by double sided tape, and another layer of masking tape since fibreglass sticks to the paper better than exposed foil.
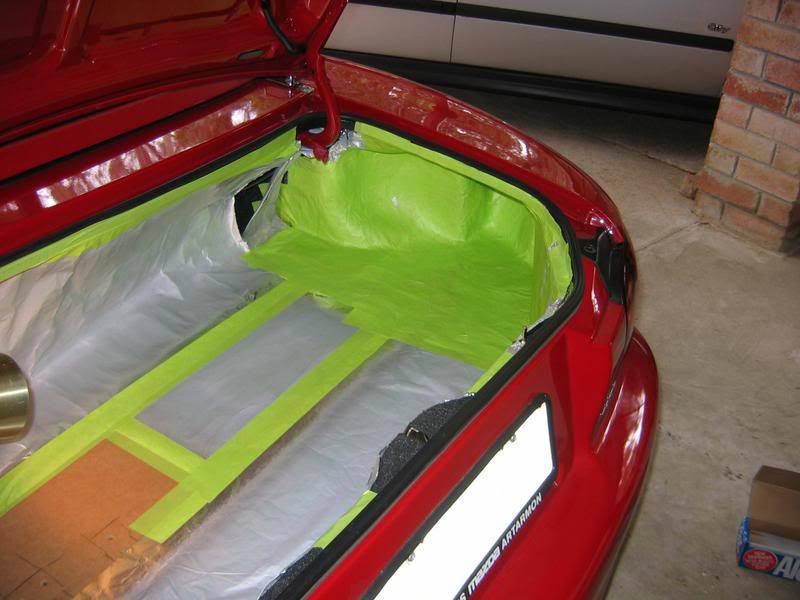
2. First layer of fibreglass. Found that the easiest way was using strips of matting about 5x30cm starting from the bottom and working up. Resin applied using a paint brush in a dabbling motion (imaging trying to use the brush end to stab the matting into position).
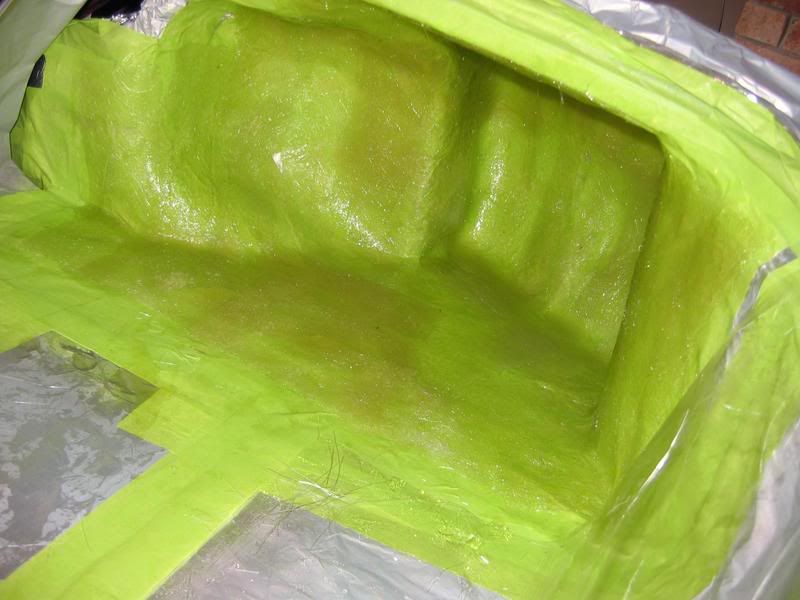
3. The mould was removed, here you can see how the foil was used making it easier to remove.
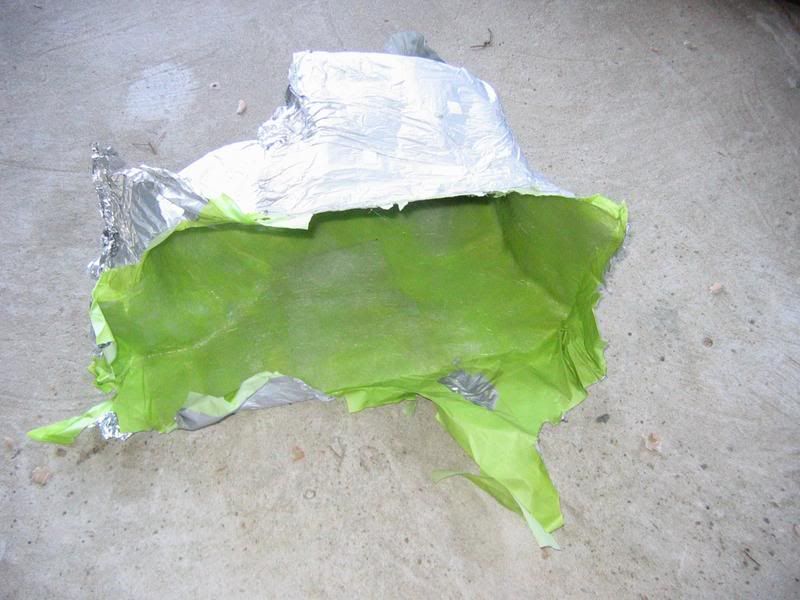
4. After removing the foil and masking tape the mould was revealed and test fitted.
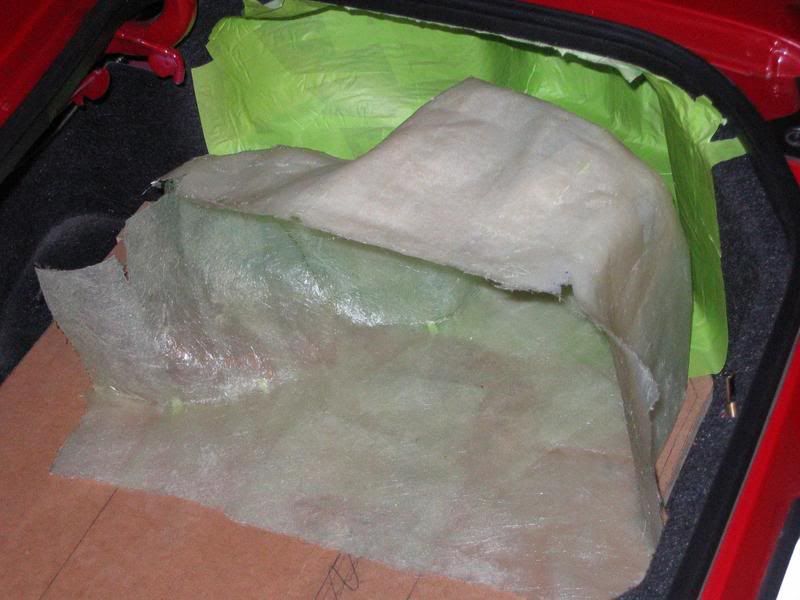
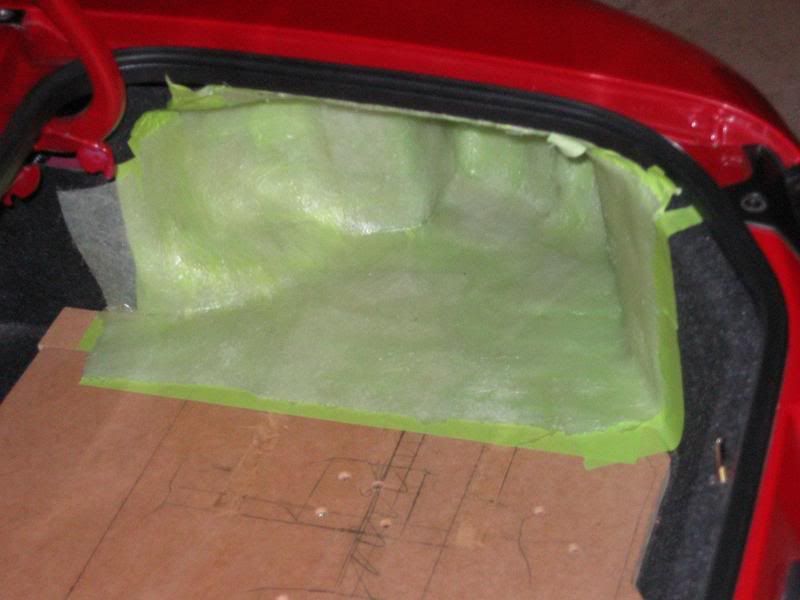
5. Skipped a few steps here, rings of MDF were made up, one for the sub to mount onto and another to go around the outside edge for a flush fit, these were then held in position using scrap pieces of MDF and a hot glue gun. Covered in a layer of flexible fabric stretched over the surface to be glassed and held in place but more hot glue, test fitted to make sure the boot would still open and close without problems. After all this a layer of resin was applied to the fabric without any fibreglass matting.
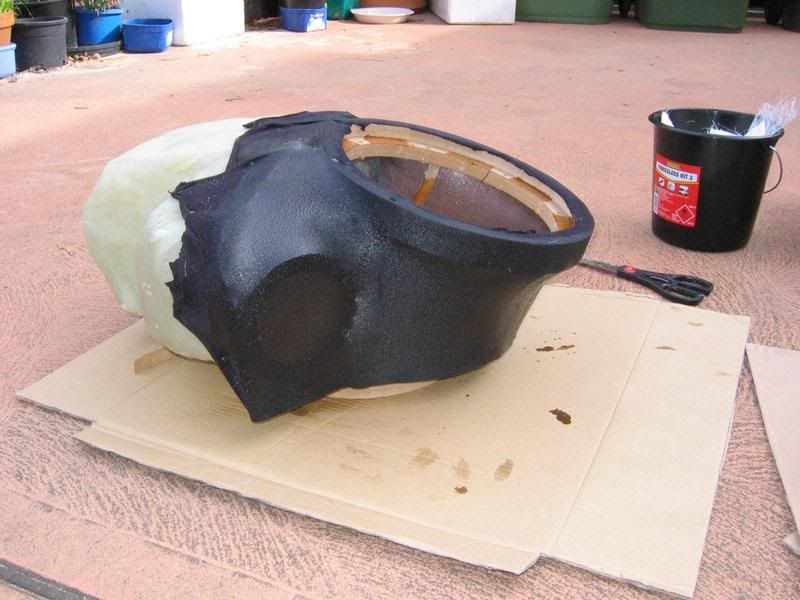
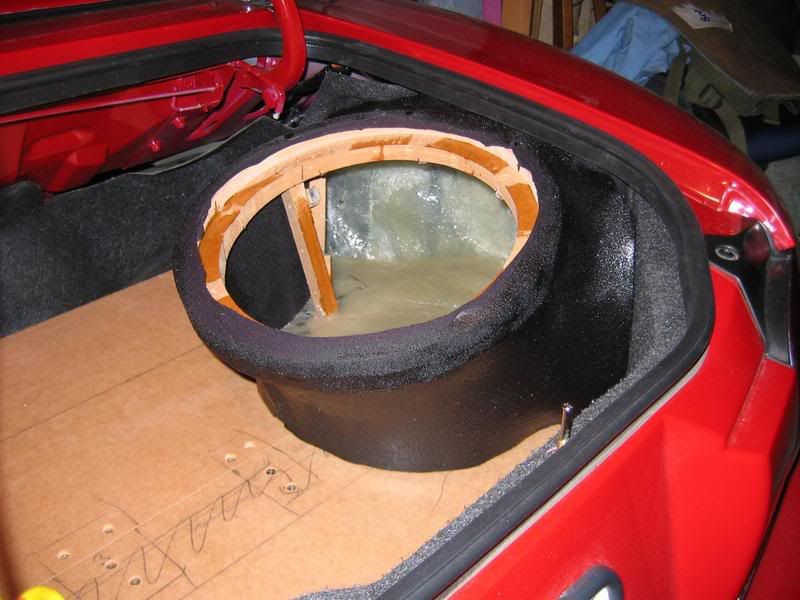
6. Many layers of fibreglass added to improve strength, most layers added from the inside via the sub hole to prevent adding to the exterior dimentions of the enclosure and comprimising the already perfect fit. Volume checked using filling from a bean bag.
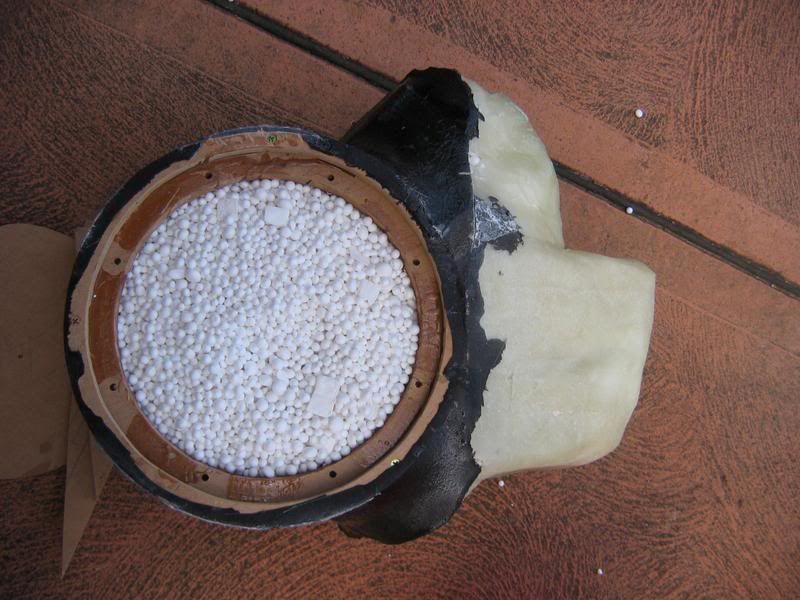
7. This photo highlights how the enclosure manages to take up minimal space while still having adequate internal volume.
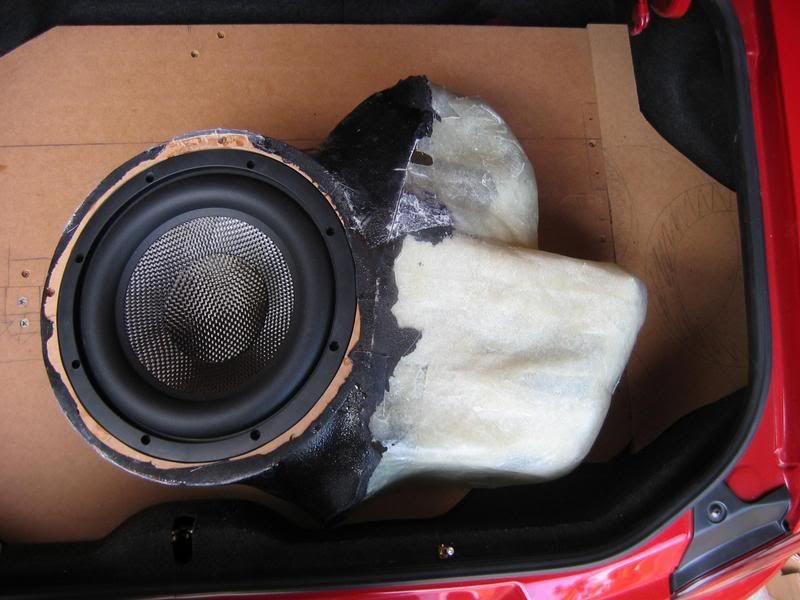
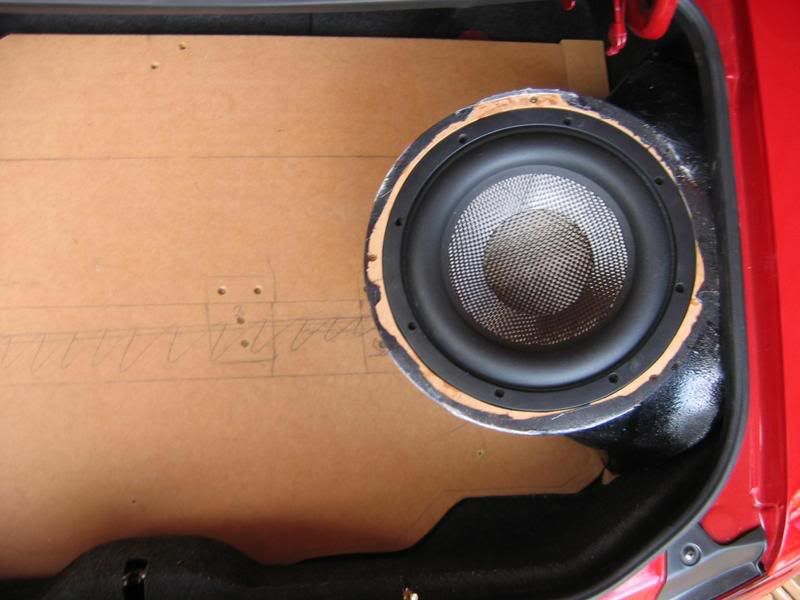
8. More layers of fibreglass added and a hole cut for the port.
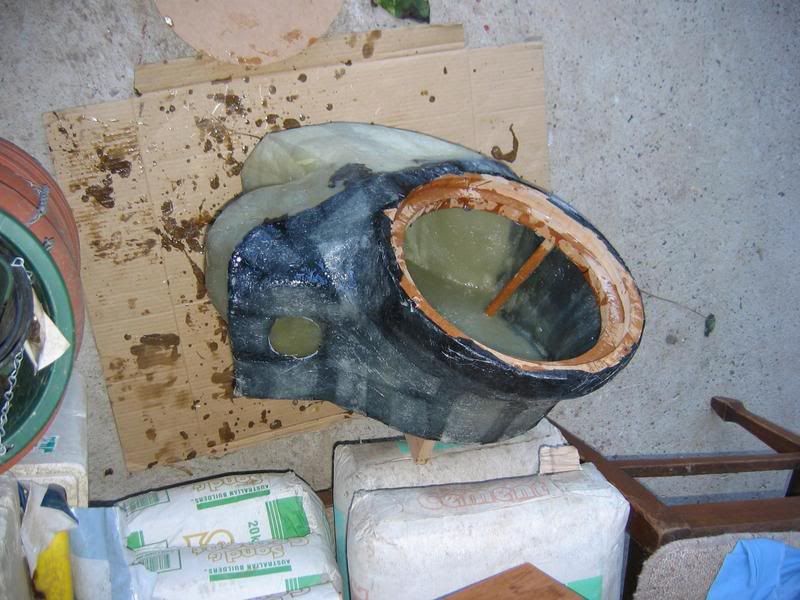
9. port added and a quick mock up with the sub in place.
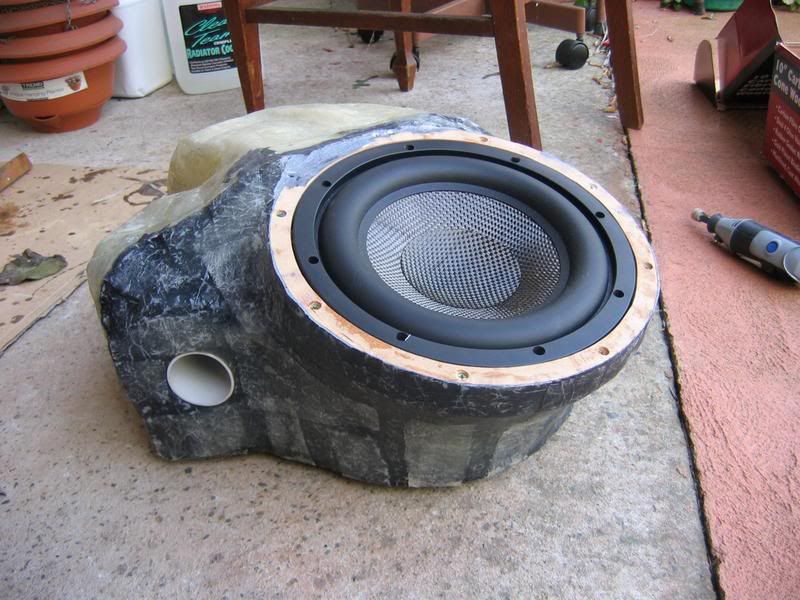
Tools required
Jigsaw for cutting MDF
scissors for cutting fibreglass matting
Dremel Router tool with sanding and cutting heads for trimming fibreglass that has set
Face mask, protecting from fumes and dust from fibreglass cutting and resins
Rubber gloves again protection from resin and fibreglass dust (it's itchy)
Things I learnt from all this
Buy from the specialists, Bunnings was great for getting the MDF and router but not so great for fibreglass 1kg was ~$55 at bunnings, in comparison 4kg with brushes mixing trays and great advice was ~$50 from FGI, a fibreglass company
There is more coming, the surface still needs to have more aesthetic appeal, amps need to be installed, and false floor covered.