MattR wrote:Mark, and everyone else reading this thread, the strut brace will make a difference.
As the brace does more than just help with forces put through the suspension. The double "A" arm design the MX5 uses looks suspiciously like the early Ford suspension used in Mustangs and Falcons from the 60's. A lot of the Mustangs had bracing from the strut towers installed by the factory.
The bracing of the strut towers is not just for the suspension it is for stiffening the whole chassis.
My explanation may ramble a bit so be patient. I am also not an automotive engineer but have been racing cars since the late 80's, so I hope a little knowledge in car preparation has rubbed off from various very smart people who have helped and mentored me over the years.
To start at the beginning, good chassis preparation will make sure that the suspension works as intended. That is the chassis geometry will behave as intended by the designer through its full travel, body flex will not introduce twisting or changing of the suspension mounting points relatively to each other which then change geometry unexpectedly and then the performance of your suspension.
Have a look at race car chassis, open wheelers and sports cars plus touring cars, NASCAR, DTM and the V8 supertaxis. The chassis are built to be as stiff as possible to provide the best platform possible for the suspension.
Open wheelers and sports cars started off as "space frame" chassis, think the Maserati bird cage cars, Lotus 7 cars and so on, plus the Siver Arrows of the '30's.
I personally had a Turner Sports 1300 as my first proper race car. A space frame chassis that was very stiff and not a lot of consideration for the driver over the other more important bits such as suspension mounts and engine, gearbox. The suspension was simple double wishbone on the front with proper coil over dampers and a 4 link rear end, again with proper coil over damper units, in may case Spax brand. The car could be jacked up at the front corner on the chassis and the diagonally opposite wheel would be the only bit still on the ground.
As technology advanced the chassis construction of race cars moved away from space frames to monocoque tubs in the 70's made out of aluminium and aluminium honeycomb. Even today the principle is the same, just the materials are now more exotic and stronger, ie carbon fibre, and exotic alloys. The advantage of this is the stiffness is a lot more than a space frame. Also it allowed constructors to use the engines and gearboxes as stressed members in the car, again aiding chassis stiffness. In fact in some cases the cars were too stiff and it may be argued that the construction may have contributed to injuries suffered by drivers in some crashes.
In the world of touring cars, NASCARS have morphed into very thick space frame chassis that a silhouette of another car shape is draped over the top of it. DTM cars are basically carbon fibre tubs that have the suspension bolted onto. Our V8's are again a space frame to which a body is glued and riveted to. The last generation of cars were built up from the roll cage. The only production bits used were a heavily modified floorpan, heavily modified firewall, a pillars and modified roof. An example of the "kit car" nature of this is when the Queensland MX5 club toured 888 racing just after they announced the switch from Ford to Holden. They had a ride car that was just completed and were in the process of converting it to a Holden. All they had to do was replace body panels. The only way you could pick that it wasn't built as a Holden was to have it parked next to one of the Commodore race cars and it was 50mm taller. All this is done to get the chassis as stiff as possible to provide the best platform on which to bolt the suspension so it will work the best it can.
Another example in chasing chassis stiffness in V8 supertaxis is the "Larry bar" used in the earlier generations. The bar diagonally across the windscreen, so famously shown at Bathurst when Craig Lowndes had the tyre bounce through the windscreen, was not there for driver safety it was there to stiffen up the chassis, which it did, a lot. If it didn't then no one would have added the extra weight to the car, especially that high up in the chassis. The benefit in having that piece of pipe added to the car would have to have outweigh, excuse the pun, the penalty of the extra weight and fractionally raising the centre of gravity of the car for every manufacturer to incorporate the bar into the cage. Remember this was in the days when the chassis still had some freedom in construction.
So now, onto why chassis bracing is important to an MX5...
Basically the car has a few things going against it to be a good platform for a race car.
First an NA is over 20 years old, any NA chassis can be basically said to be worn out, it has 20 years worth of fatigue in it.
Second, the body is a convertible, there is a big bit missing that adds a lot of stiffness to the car.
The technology of the time when the chassis was designed is very different to what is available now and is shown when comparing the stiffness of an early model to the latest model.
In simple terms, spending a bucket load of money on the best suspension available for your 20+ year old car is of no benefit unless the chassis is prepared to make use of it. If the chassis is as floppy as Raggedy Andy's flaccid penis then the suspension is going to flop around with the chassis and not provide the improvement to performance it should.
That is why there are so many solutions for bracing the MX5 chassis, some work better than others. Even the factory made strut braces for the car and when the NA6 was updated to the NA8 extra bracing was fitted by the factory.
On my 5 I have done the following to improve chassis stiffness, front struct brace and torque bar roll bar. It makes a bit of difference to how the car handles, but I could do so much more to make any changes more effective to the handling of the car. To do the job properly, I would look at a full welded in cage, seam welding and also some under body bracing to get the basic car as stiff as possible so the suspension can do its job better.
If you look at most MX5 race cars built, how have they been done, especially for 2F? Basically get the carpet out of the car, remove some trim and bolt a half or full cage into the car.
Does anyone strip the car down to an absolute bare shell and then take out all the sound deadening clean all the seams out and then weld them up?
When the cage is built is any consideration given to making sure the elements in the cage are tied to suspension mounting points? Again this aids in stiffening up the chassis and minimising the movement of the suspension mounting points allowing the suspension to work better.
As an example of what I would consider reasonable chassis preparation here is what I have done to my S14 in building the cage and also seam welding the shell where required.
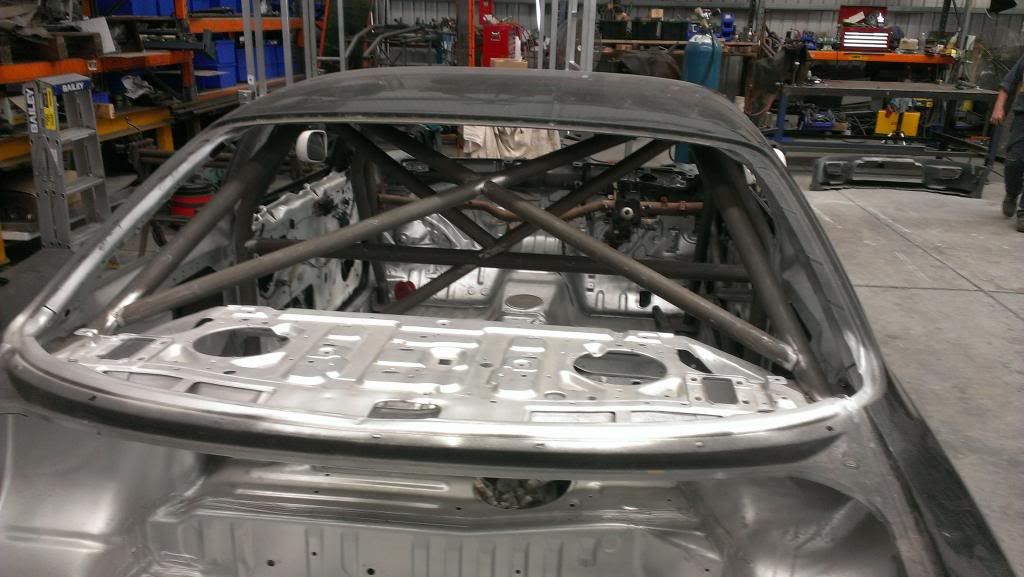
This is a basic overall view of the ROPS being built in the car. The rear legs tie into the rear subframe mounting points. The rear stays also tie into the strut top mounts in the rear parcel shelf structure.
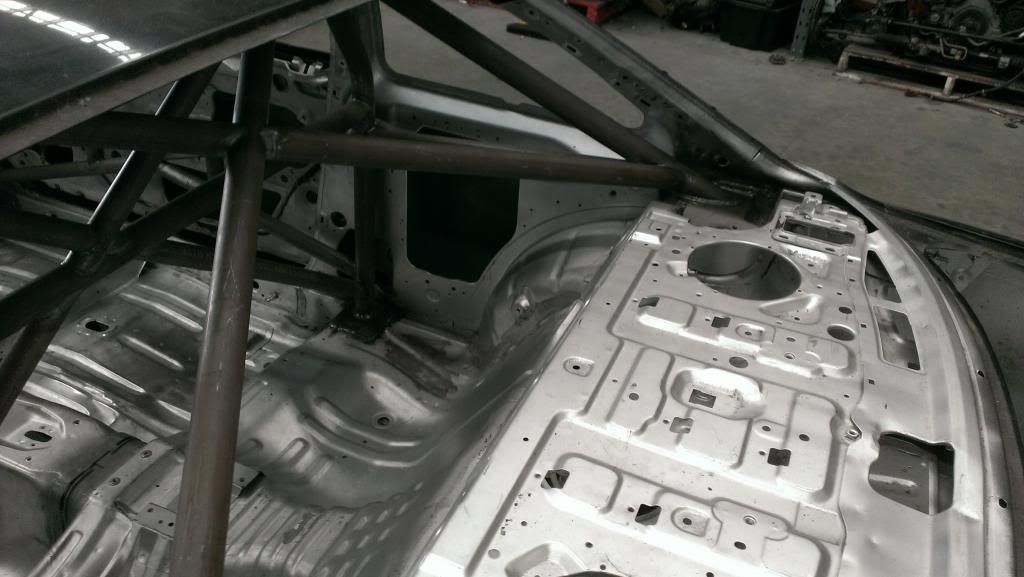
The cage is also tagged to the a and b pillars to add to the stiffness of the shell.
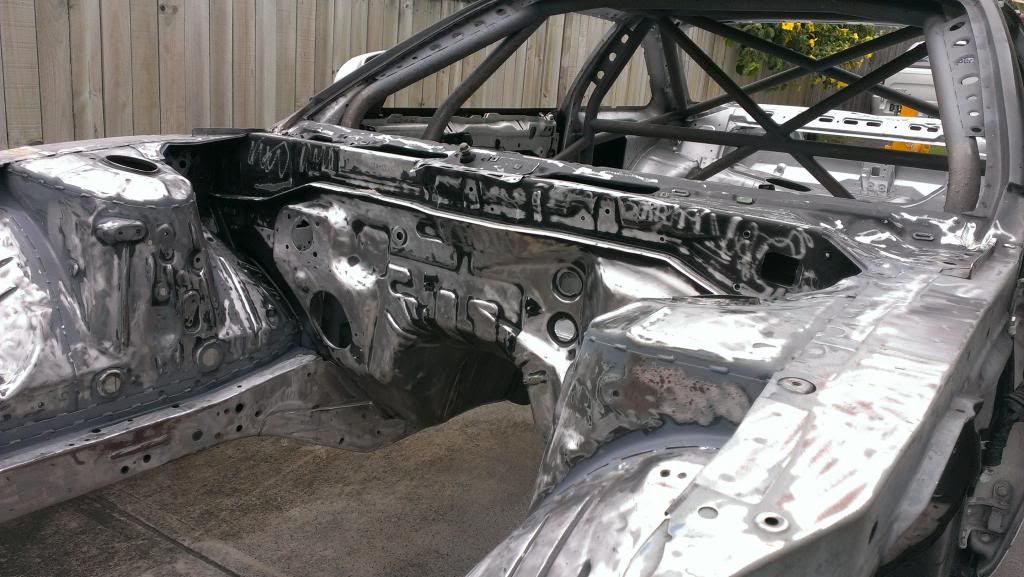
On top of the cage work, as the rules for Production Sports cars don't allow me to have the cage through the fire wall to tie in the front suspension, I have had the front seam welded, plus the two seams in the floor pan running across the car. I will also be fitting a front strut brace as allowed by the rules, so unfortunately I won't be able to triangulate to the firewall.
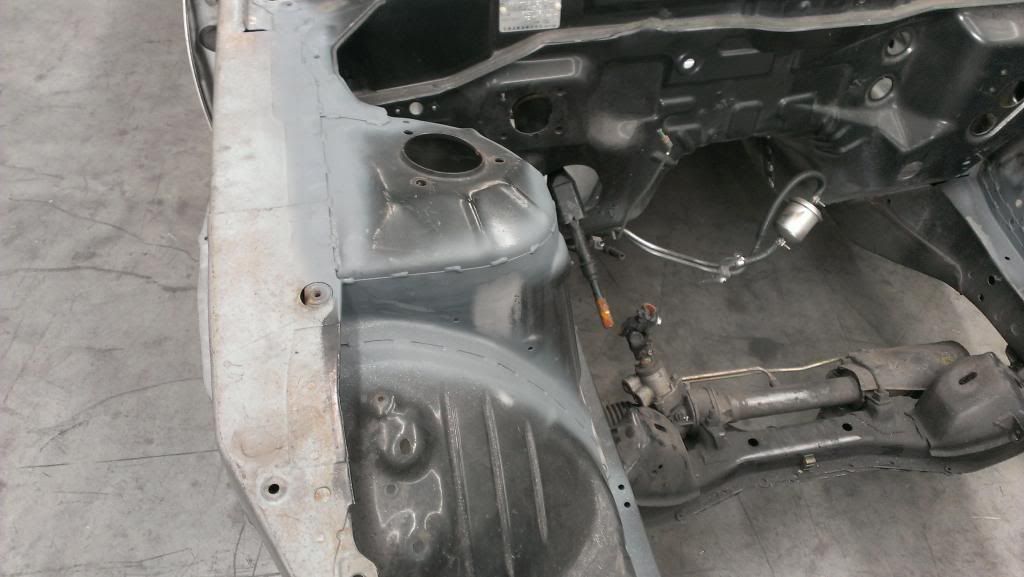
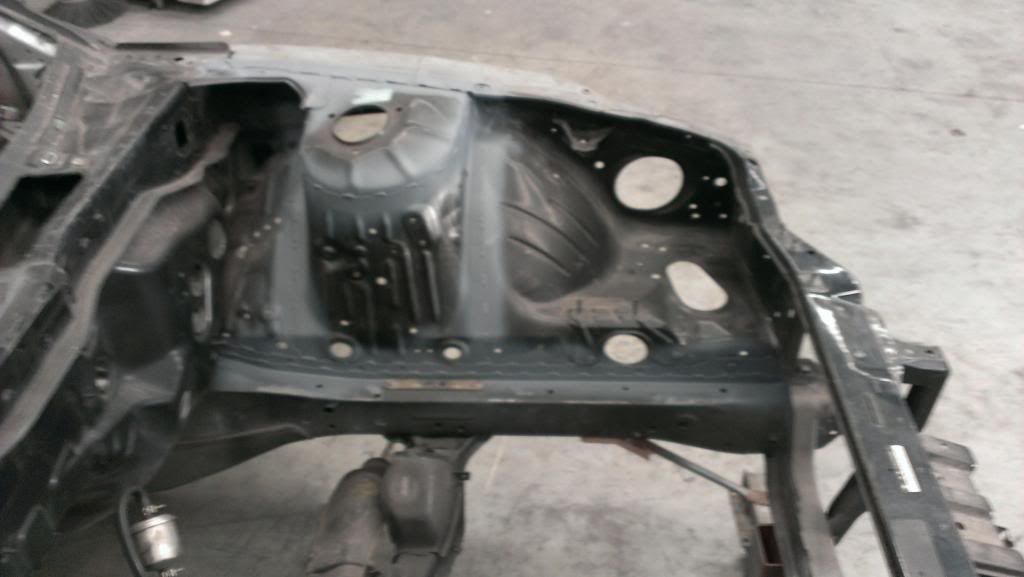
The end result of this work is a car that will respond to suspension tuning a lot better than most. Rather than the body flexing preventing the springs and dampers from doing their job or the suspension geometry changing in unexpected ways with the change in shape of the body and the twisting of suspension mount points I will have a nice stable base for the suspension to work.
This means that when I make a change I know what will happen and I can actually fine tune the suspension to the point where very small changes will make a difference.
As another example of how chassis preparation makes a big difference is to compare the two Datsun Zeds I owned and raced.
The first was a 260Z 2 seater, built fior rallying, I bought it after about 3 seasons at State championship level events. It had a half cage tied into the rear rear strut towers, but no other real preparation. After three years of rallying the shell could only be described as tired, some would say well and truly flocked would be a better description. I raced this car in what was the precursor to 2F in the early 90's. It was a horrible handling car that taught me a lot about about driving and how to drive around a problem. When we jacked up the car at either the front jacking point under the sill or by the lower control arm only that front wheel would be raised. If the bonnet or doors were open they couldn't be closed and vica versa. There was no tuning the suspension you threw what shocks were known to work and slightly stiffer springs and away I went.
The second Zed was a 240, an early light weight shell, but it had a full cage and seam welded throughout the engine bay. This car was a world of difference in behavior on the track. The suspension could be tuned for damping and also spring rates. I could make a 20lb/inch change in spring rate and you could feel and quantify the difference in handling. The damping could be changed and again you could feel the change and also quantify the change against the clock. Because the chassis was stiff and the suspension worked properly, consistent times could easily be achieved when testing and making changes to the car.
When jacking up the car in the same locations as the 260, the doors could be opened and closed. The bonnet was a fibreglass bonnet held on by 6 pins so no comparison there. All wheels bar the one opposite the jacking point would lift off the ground at the same time as you jacked the car up.
In summary, for mine it doesn't matter what suspension is used, proper bracing and preparation of the chassis for stiffness is essential to get the best performance from the suspension. As most time is made on the track through the chassis, in Mark's car I would sacrifice and drive around the torque dip caused by the intakes to get the more beneficial performance and better times that comes from having a stiffer chassis.